Depot charging vs. interval charging
Depot charging As the name implies, depot charging involves charging electric buses at the depot location. Here, charging is usually done with a plug-in system, in which the bus is connected to a charging station by a charging cable. Charging via induction (wireless) or a pantograph (from above) is also possible, though less typical. At a depot, charging occurs overnight or during longer idle periods. Since a bus usually does not need to charge for its entire idle time, charging processes at depots can be flexibly managed in order to considerably reduce electricity costs.
Interval charging Electric buses not charged at the depot but rather in transit, at route stops or the final destination, is known as interval charging and involves pantographs, inductive charging stations or docking systems. Interval charging, also known as en-route charging, is especially beneficial for electrifying long stretches, however the short charging window requires high charging power - making it more expensive and effortful.
DC charging vs. AC charging
Another important factor to consider is the speed and power at which different charging types can charge a bus: AC or DC charging. A critical difference between the two systems is that alternating current (AC) charging systems operate using a rectifier built into the vehicle, while direct current (DC) charging uses a rectifier built into the charging station. DC charging allows for much greater charging power and thus shorter charging times. Therefore, buses are frequently charged using DC charging stations to maximize their operating schedule. The efficiency factor, battery status, temperature and age of the battery also play an important role in calculating the time needed for charging. While the condition and life of the batteries is not necessarily worsened by charging, using smart charging logic normally contributes to a longer battery life.
Depot charging deep-dive
To avoid over spending on an infrastructure build or risk falling short of a bus’ charging needs, creating a depot charging location requires detailed, forward-looking planning. Here are a few questions to consider.
Does every bus need its own charging station?
Individual charging stations are often set up for each bus, but in reality not every bus needs its own station. In many cases, installing charging stations with multiple charging ports is a more viable option, as it can reduce the investment costs and space requirements of the overall charging infrastructure. As a rule of thumb, The Mobility House recommends providing each bus with its own charging port to avoid the time-consuming shuffle of plugging in, unplugging and re-parking buses. Pro tip: A bumper buffer helps keep the charging electronics safe from accidents. Think steel protection, a raised approach board or a wraparound protective band similar to those used on gasoline pumps.
How do space requirements, transportation schedules and operational processes factor into charging infrastructures?
Designing the right charging infrastructure heavily depends on the space requirements of the depot. Evaluating the site’s usable space will dictate the possible number of charging stations, cable lengths, placement for switching cabinets and more. With two main strategies for parking, placement of the electric buses also determines how flexibly the charging ports can be used: A herring bone placement allows for more flexibility in relation to the use of the charging ports while an end-to-end placement means that parking slots need to be filled from front to back. With end-to-end parking, which charging port connects to which vehicle is determined by the time of arrival.
Which is better: pantographs or charging cables?
Many operators prefer charging with pantographs at the depot to avoid dealing with charging cables. To save space, it is also possible to install charging hardware above ground-level. But remember, a DC charging station often weighs one to several tons.
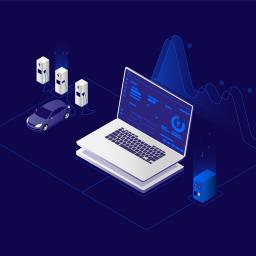
Smart charging and energy management
The Mobility House has simulation software that can analyze the number of buses at a depot, fleet schedule and charger specifications to help fleet operators build a charging infrastructure specific to their needs. Once the buses are up and running, The Mobility House’s charging and energy management system, ChargePilot®, then manages and optimizes the flow of electricity for a depot’s many charging stations to ensure buses are charged when they need to be at lowest cost. To learn how to optimize your electric fleet operations with The Mobility House’s smart charging and energy management solution, contact us at [email protected].